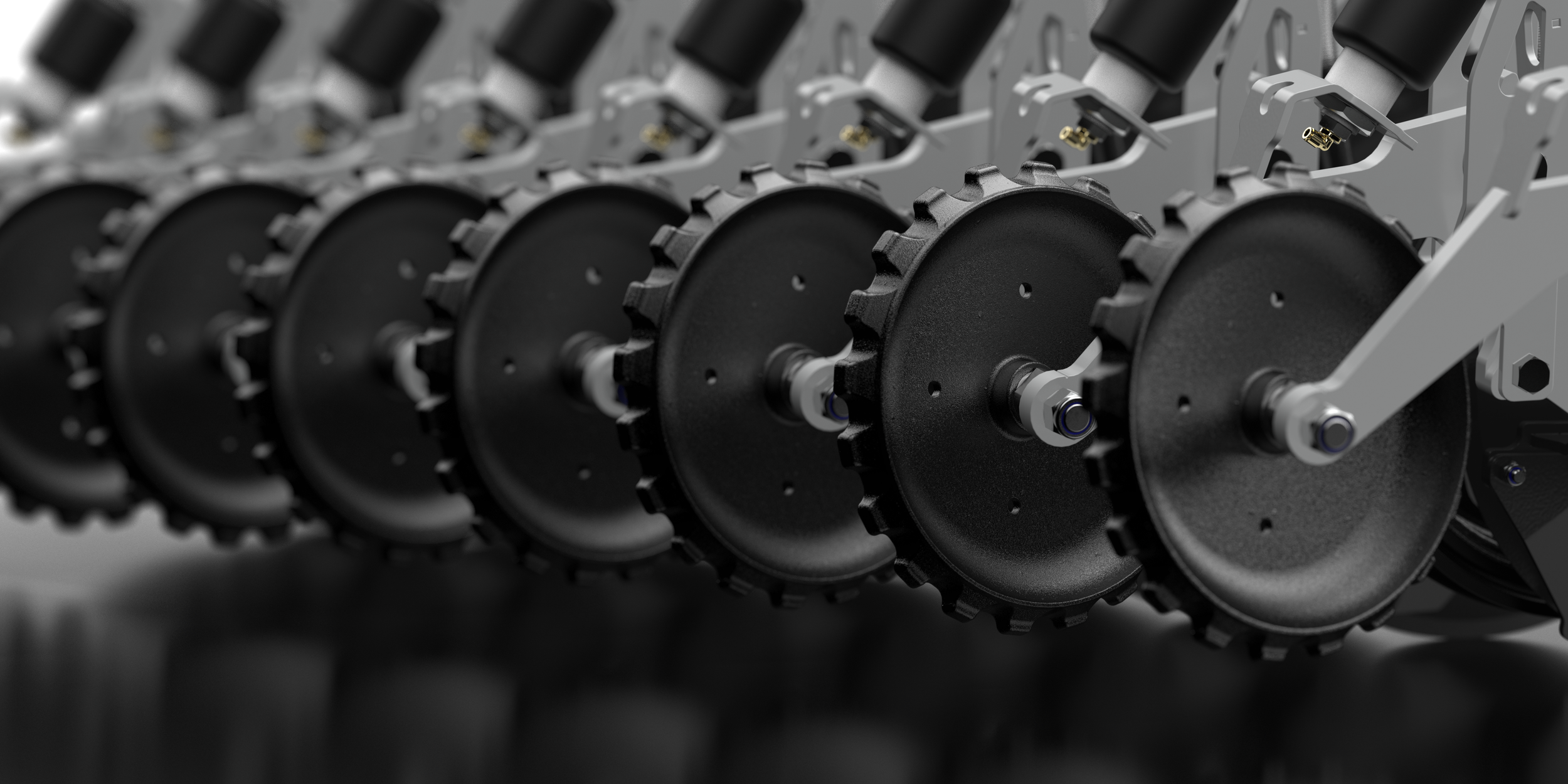
DSX
Designed and developed with the specific aim of overcoming the challenges of seeding with a no-till disc drill, the DSX enables farmers to accurately place seed in the perfect growing environment with minimal soil disturbance.
NO-TILL SEED DRILL
Features the leading no-till disc coulter on the market.
The 4m modular frame can be extended to 4.8m, 5m, 6m, 6.4m, 7.2m, 7.5m and 8m.
Choice of 16.7cm, 18.7cm, 20cm and 25cm row spacings.
Optional row cleaners reduce hairpinning.
Highly configurable multi-hopper set-up.
Uniquely angled undercut disc ensures consistent penetration and closing even in the hardest conditions.
In cab controlled pneumatic closing system.
Parallel linkage for optimum contour following and depth control.
In-house liquid fertiliser solutions.
Avadex toolbar.
Various closing wheel options available.
*New 8m & 9m launching in 2024*
WHY CHOOSE THE HORIZON DSX?

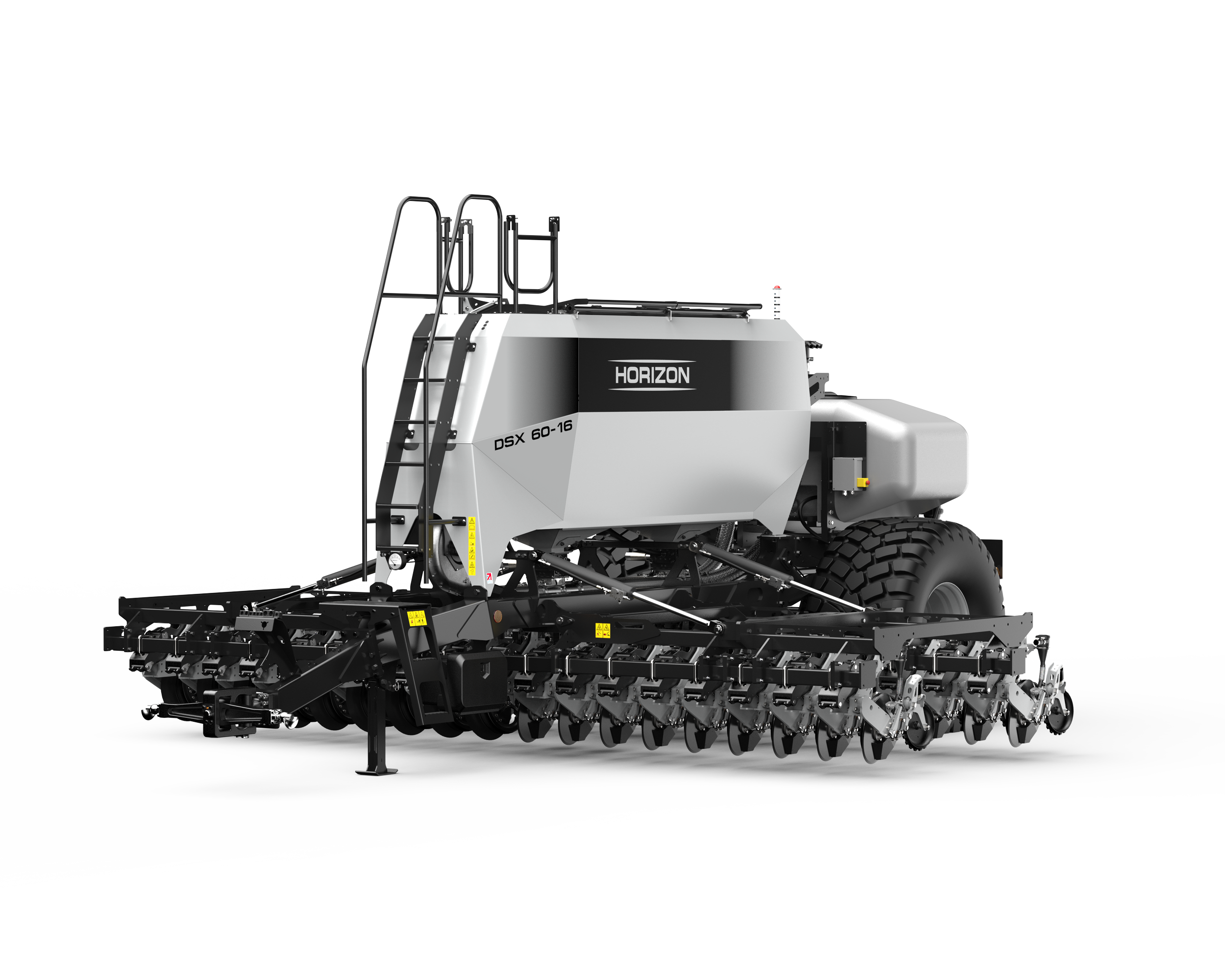
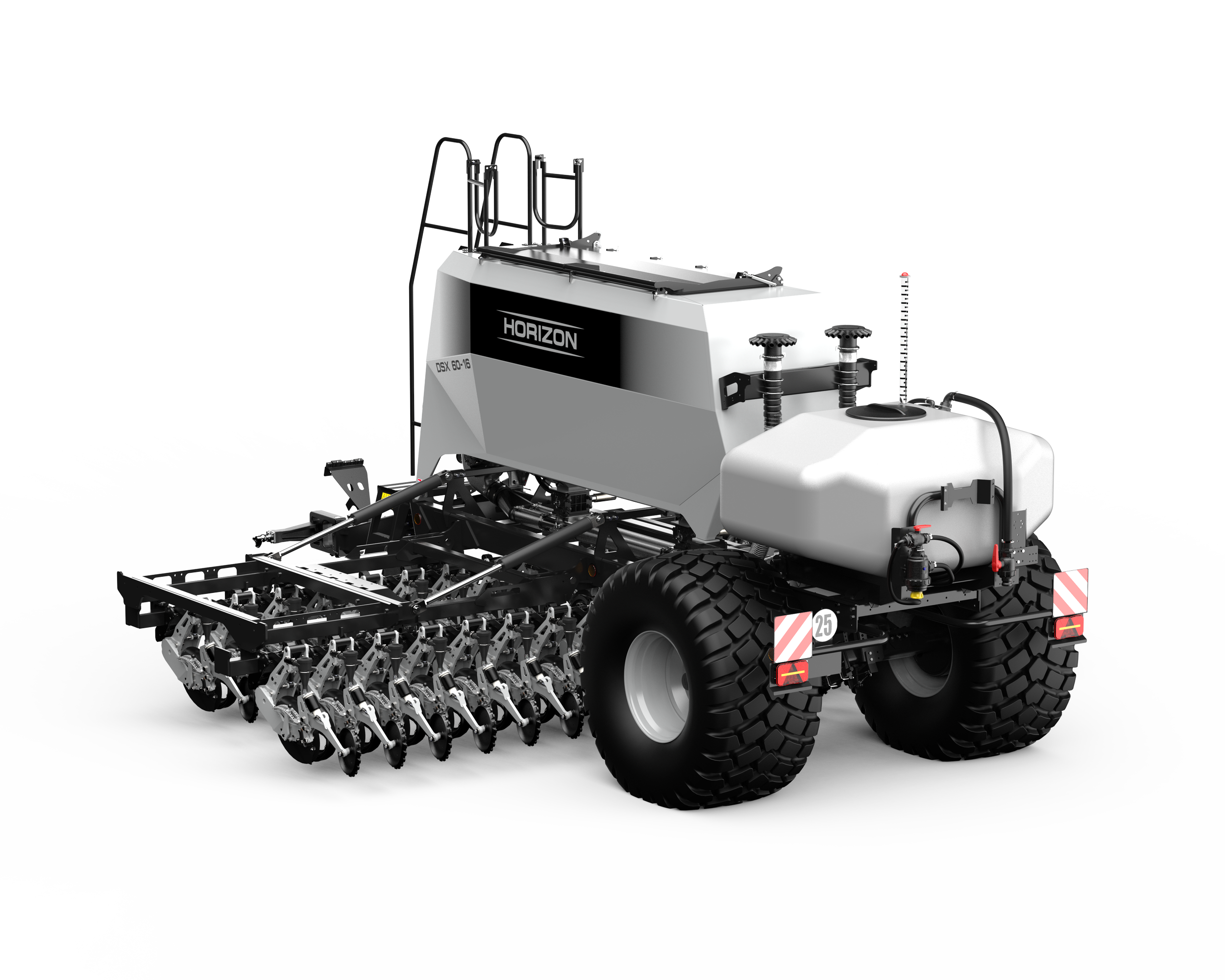


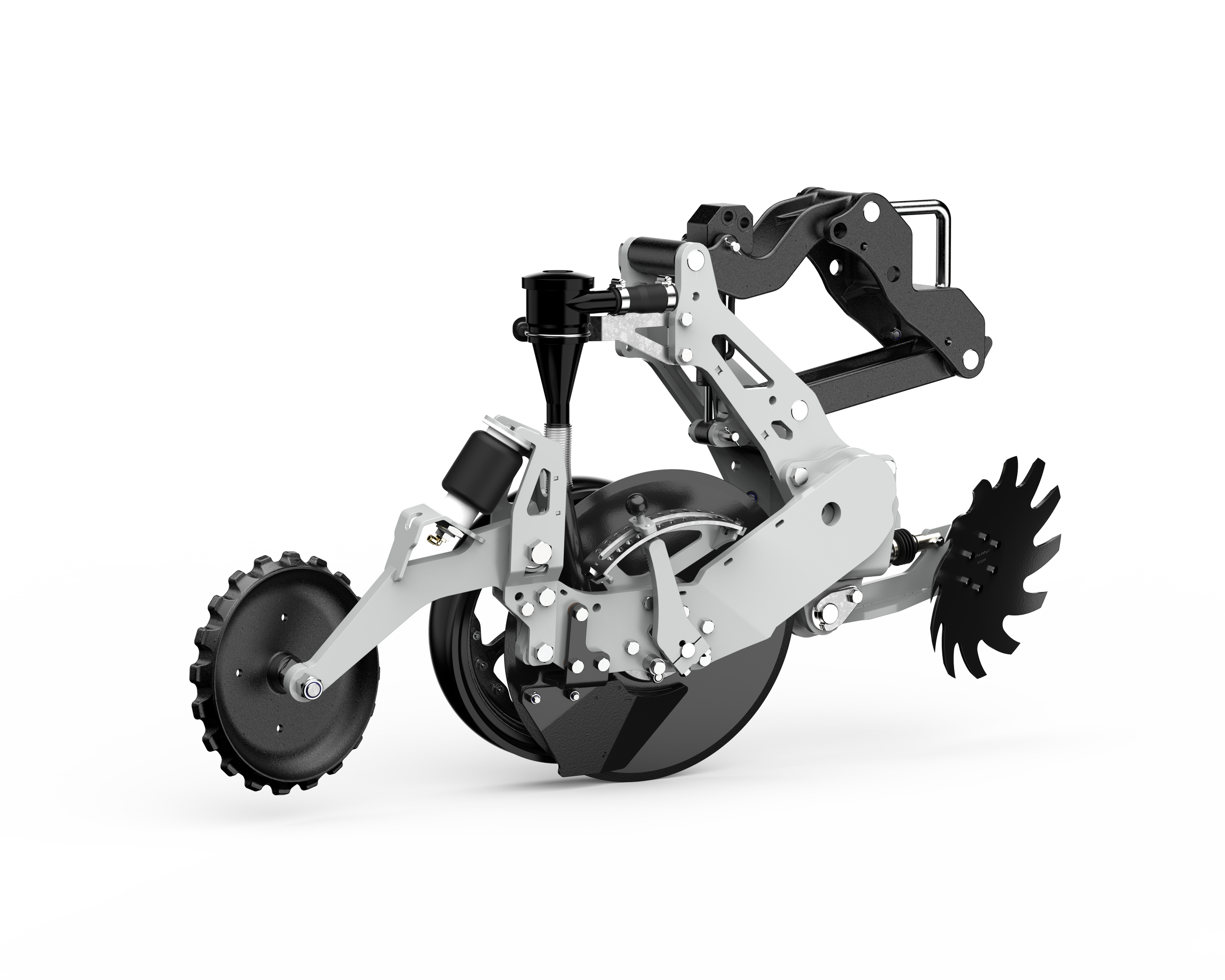

SEEDING CONFIGURATIONS
Sowing all rows
Sowing with double row spacings
sowing two different products
KEY FEATURES AND BENEFITS
-
The 4 / 4.8 / 6 / 6.4 / 7.2 and 7.5m DSX drill models utilize a modular frame design, enabling our customers to easily expand the width of their machine should they need to cover a greater area in the future.
-
The 2nd generation row unit features an undercut disc that is capable of penetrating the soil more effectively than a traditional vertical disc drill. As a direct result, the DSX will always deliver consistent and accurate seed placement, even in the most challenging conditions. The angled disc pulls itself into the ground, requiring less downforce and resulting in less compaction to the soil surrounding the seeding zone.
The seed is dropped under a flap of soil, making it easier for the press wheel to completely close the seeding zone. This process also captures humidity at the point of the slot being closed, creating a better environment for the seed to successfully germinate.
The disc angle on the 2nd generation row unit has been reduced by 10 degrees from the first generation. This development has helped to eliminate any potential soil throw and allows faster forward speeds in light or cultivated soils. Typical forward speeds are between 9kph and 12kph.
-
The 2nd generation DSX row unit utilizes a parallel linkage that offers 300mm of contour following travel. Each coulter is pressurized by its own individual hydraulic ram, the pressure for which can be centrally adjusted from the cab, allowing the operator to quickly and easily set the pressure to suit soil conditions.
0kg to 350kg of downward force can be applied per row unit (this will vary between drill widths and the number of row units fitted), enabling the DSX to consistently place seed at the correct depth, even in extremely dry and compacted conditions.
The 2nd generation row units depth wheel is positioned directly in line with the seed outlet, offering market leading depth control. This is especially important when shallow seeding. Depth can be easily adjusted in 5mm increments, allowing for perfect seed placement.
-
The pneumatic closing system offers between 6kg and 90kg of closing force, which gives the operator the flexibility to adjust the closing pressure from the cab, ensuring perfect closing across a wide range of applications, soil types and conditions.
The closing wheel can be adjusted to be more or less aggressive, achieving perfect slot closure, no matter the conditions.
A variety of closing wheels are available to suit differing soil types and conditions. Closing wheels can also be lifted out of work when not required, for applications such as bean drilling in wet conditions.
-
CleanSweep technology allows the operator to adjust row cleaner down pressure from inside the cab, resulting in less ‘hairpinning’, a higher plant count and more uniform germination. Row cleaners can be locked out of work when not required.
-
The DSX offers a multitude of seeding possibilities, with the ability to run up to four granular hoppers and one liquid tank.
Product placement is simply adjusted with a lever, resulting in configurations that facilitate different products being placed together in all the rows (seed and fertilizer), with every other row shut off (OSR on wider spacing) or alternative rows for different products (companion cropping or large and small seed cover crop mixes).